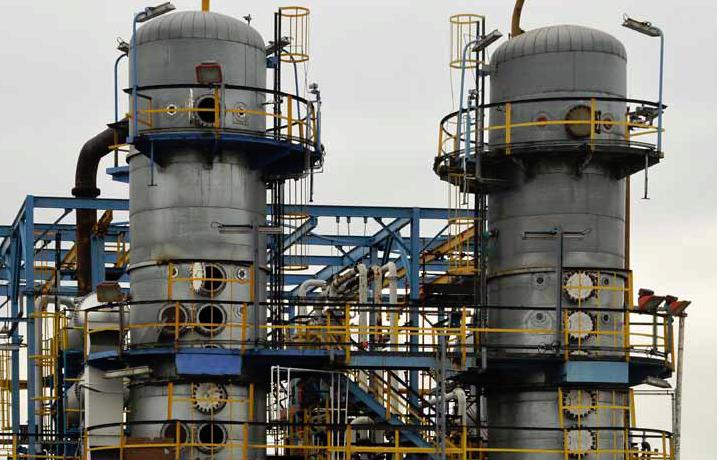
Research and development is not only the hallmark of Karbochem’s success but also its greatest opportunity for the future, as Gay Sutton discovers from commercial director and chairman Dr Abraham Brink.
Johannesburg-based chemicals company Karbochem, the only manufacturer of synthetic rubber in Africa, has been operating since 1964, but a management buyout from global chemicals conglomerate the Dow Chemical Company in 2003 heralded the start of a new era focusing on new product development, process improvement and environmental best practice.
For the team that led the buyout—Dr Abraham Brink, Duncan Blackburn and Piet Steenkamp—the opportunities were irresistible. And interestingly, they were a reversal of the usual take on economies of scale. “Most global conglomerates like Dow will put a fairly hefty head office charge on their operating divisions,” explains Brink, now Karbochem’s commercial director and chairman.
By operating with a much smaller level of management, Karbochem has been able to operate under considerably reduced overheads, therefore increasing profitability while keeping prices pegged at competitive levels. “And we are certainly very pleased that things have turned out so well,” he continues. “We’re not wildly profitable, but at this point in time we’re pleased to say we’re doing much better than we would have if we had put our money in the bank.”
The company is structured around three autonomous operating entities—Karbochem, Synthetic Latex Company (SLC) and Orchem Trading—which are drawn together under the umbrella of Karbochem Holdings. Of the 340 staff employed within the group, some 320 work in Karbochem, but each of the three entities has retained its original identity since the buyout. “We have chosen to do this because each of our three product streams has a unique set of parameters requiring a dedicated marketing and management team. So each company is managed independently and has its own board of directors.”
Karbochem, by far the largest part of the company, manufactures synthetic rubbers for mainly the tyre-making industry and operates from two manufacturing sites: one in Sasolburg, Free State, and one in Newcastle, KwaZulu Natal. SLC manufactures styrene acrylates, pure acrylics and carboxylated styrene butadiene latices from the Karbochem facility in Sasolburg. Orchem, a trading company dealing in rubber chemicals and related products, operates out of Durban; however, the group has offices in Bruma near Johannesburg for the sales and marketing functions of each of the three companies.
Research and development (R&D) has long been embedded in the Karbochem operational ethos and is an essential element in the company’s strategy for growth. New product development dates back to the early 1990s when the company, then owned by Sentrachem, was unable to procure the technology it required to produce neodymium BR—a specialist synthetic rubber with highly desirable properties for tyre manufacture. The company resolved the problem by developing its own product and processes, and these have been so successful that the neodymium plant is running to capacity and cannot satisfy all the market needs.
In recent years, however, the focus of the R&D has shifted somewhat towards the needs of SLC. A significant amount of investment has gone into the primary R&D facility in Newcastle and a satellite facility at Sasolburg, and from here the company has developed a unique in-house range of styrene acrylates and pure acrylics—binders used primarily by the paint industry. “SLC has always produced styrene butadiene latexes, but because the chemistries of the two new product ranges are very similar, we made the decision to focus our efforts on producing them all at the same plant. We’re now expanding into the paint market and we believe we can gain a much larger market share. The products also have applications in carpet manufacture, the construction industry, and to some extent in the manufacture of glossy paper,” Brink says. “The gloss is essentially a very thin layer of rubber on the paper surface.”
The company continues with its programme of R&D, researching, producing and testing new products to meet specific market needs. And it is here that Brink sees the most significant opportunities for growth. “As far as the rubber side of the business is concerned, our long-term view is to optimise the capacity we have. But because the major raw materials are imported it makes very little sense to expand significantly here in South Africa. On the latex side of the business, however, the situation is totally different,” he says. “We have ample capacity at the plant, and we hope to gain a much larger share of the paint and carpet markets. Ultimately, we aim to reach full capacity.”
Considerable improvements have already been achieved on the rubber side of the business, through a programme of process optimisation and investment. The Sasolburg plant, for example had a designed capacity of 20,000 tons when initially commissioned. “Now, depending on product mix, we have a capacity of up to 35,000 tons,” Brink says. “Meanwhile, our neodymium plant in Newcastle was originally producing 25,000 tons and we have increased that to 35,000 tons. Moreover, we believe that with some debottlenecking we could further increase the output to 40,000 tons. Our other rubber plant in Newcastle has the nominal capacity of 30,000 tons, but as we run such a large range of products it’s currently operating at about 25,000 tons.”
Quality has always been a strong focus across all operations. All plants are ISO 9001 certified, being regularly audited by the South African Bureau of Standards as well as by the global tyre producers who are the company’s major customers.
Since taking over the company, Brink and his fellow directors have also worked to improve the environmental performance of the manufacturing sites. The boilers at the Newcastle plants are coal-fired, as is common in South Africa, and the latest technology has been installed at each to minimise the emission of gases and particulates into the atmosphere.
“We have also done a lot to rectify historical problems at the plants, and we believe we have not created any new ones,” Brink says. For example, there were a number of evaporation ponds in use for the evaporation of effluent. “We have cleaned them out, physically removed them and banned their use in the future. At the Newcastle plant we have an installed effluent treatment system and are running almost effluent-free. At Sasolburg we’ve made arrangements for Sasol to treat our effluent at their huge treatment plant.”
Not only does Karbochem have bright prospects for future growth, it is also doing its bit for the environment. “We try to be a good citizen,” Brink concludes.
DOWNLOAD
KarboCHEM_MAY11_emea-bro-s.pdf